Subscriber Benefit
As a subscriber you can listen to articles at work, in the car, or while you work out. Subscribe NowMakers of everything from faucets, furnaces and cars to door locks, lawn equipment and medical devices use microchips as the brain for their products. And silicon semiconductors build those microchips.
But a global semiconductor shortage, driven in large part by pandemic-related factors, is forcing many central Indiana manufacturers and distributors to broaden their supply base and forecast their needs longer term, along with hoping for federal aid from the president’s infrastructure proposal.
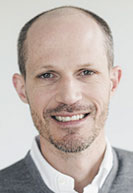
“At Subaru of Indiana [in Lafayette], a car comes off the line every 57 seconds and it can have over a thousand semiconductors in it,” said Bryce Carpenter, vice president of industry engagement for Conexus Indiana, which promotes the state’s advanced manufacturing and logistics industries.
“A semiconductor takes about 3-1/2 months to make. Right now, because of demand, that’s six months,” Carpenter said. “This is not a normal production of a piece of equipment.”
According to New York-based Goldman Sachs, 169 U.S. industries embed semiconductors in their products, and the world will continue to see an average 20% shortfall in the computer-chip supply until the end of this year.
Because semiconductor manufacturing is complicated and is dominated by only a few players, and because semiconductors in turn build complicated microchips that build complicated circuit boards that operate increasingly complicated products, the supply chain is particularly prone to disruption.
The current disruption can be traced to a perfect storm of COVID-19 limitations on manufacturing, a surprise Texas deep freeze, droughts in Taiwan, a fire at a Japanese facility, pandemic-driven consumer buying trends, overburdened supply-chain constraints on related components and other factors.
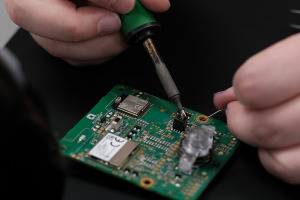
Minnesota-based TMC’s division headquarters in Carmel serves as a manufacturer’s representative for more than 30 electronics companies. It connects suppliers of semiconductors and other electronics components with original equipment manufacturers in Indiana, Michigan, Kentucky, Ohio, western Pennsylvania and West Virginia.
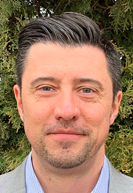
General Manager Brooks Mattice said semiconductors are increasingly crucial to a growing number of industries—from Lexmark printers, to Carrier HVAC systems, to Delta’s smart faucets and more.
“Today, 40% of your car is electronic devices, and it’s growing rapidly. … Your furnace and air-conditioning system typically has four motors, and they all have smart electronic controls driving them and making them more efficient,” Mattice said.
But meeting increasing demand quickly, even in “normal times,” is not as easy as in many industries, he said.
“You can’t just turn it instantly on. These are incredibly complex devices, and they’re incredibly complex to manufacture,” he said. “It takes really smart people to get these manufacturing processes down. You’re limited by physics. You just can’t make it happen sooner.”
Just one part of the process to prepare a silicon semiconductor for use in a computer chip can take 60 to 120 days, he said.
Longer-term thinking
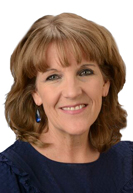
Cindy Farrer is vice president of global operations and integrated supply chain for Dublin, Ireland-based Allegion, a home and business security-product provider with an American office in Carmel.
Allegion’s electronic locks and access-control products depend on semiconductor-built circuit boards.
“A circuit board could have a few components, or it could have a hundred components. You miss one part, and you can’t make the circuit board. That makes it very risky, because you’re depending on everything coming together,” she said.
Farrer said the semiconductor shortage has forced Allegion to “sharpen up” its supply-needs forecasting.
She is already thinking about what disruptions might be caused by the Chinese New Year in February, when factories in China typically close and employees go on holiday for at least two weeks, she said.
Mattice said the industry’s complicated and funneled supply chain means a microchip might be shipped halfway around the world several times before it reaches the customer.
IC Insights, an Arizona-based semiconductor market research company, recently published a report that said the world’s top five silicon-wafer-producing companies were responsible for 53% of global supply capacity in 2019. Those companies—including goliaths Taiwan Semiconductor Manufacturing Co. and Seoul-based Samsung—are based in South Korea, Taiwan, Japan and the United States, with the majority of the smaller companies in Asia.
Carpenter said U.S. companies represent just 12% of the global supply, but President Joe Biden’s proposed infrastructure plan includes $50 billion for the domestic semiconductor industry.
Getting into the semiconductor business is no walk in the park. Opening a facility with the required clean environments takes years and costs billions of dollars. That’s another factor that slows the industry’s response to demand increases, adding to its supply-chain vulnerability.
“When the world turns, it turns quickly and suddenly,” Mattice said.
Story continues below graphic.
In late April, GM announced its assembly plants in Ontario, Kansas and Michigan would continue their semiconductor-shortage-related shutdowns through late June and into July. General Motors Components Holdings in Kokomo does make semiconductors, but not enough to supply a company of GM’s size.
For TMC and many other semiconductor-related businesses, the shortage has meant slower order fulfillment and skyrocketing costs for its customers.
“We’re on constant calls with customers trying to get more allocations, trying to expedite product. It’s taking up the majority of our workday,” Mattice said.
Suppliers absorbed three or four increases in raw materials costs before finally passing some of it on to their customers, he said. That’s resulted in some uncomfortable conversations with customers who are already waiting until September to get a shipment they’ll need next month.
Normally, average delivery time for a single component might be eight to 12 weeks, Mattice said. Now, the bare minimum seems to be 18 to 20 weeks.
“Many, many suppliers are approaching customers and saying, if they don’t place orders now, they won’t get them in calendar year 2021—and that’s for the biggest customers,” he said.
The switches, fans, enclosures and other products that Mike Lamping sells at Wisconsin-based Marsh Electronics’ Noblesville location aren’t directly reliant on silicon semiconductors, but the branch manager has seen his complementary components’ delivery times balloon from around five weeks to as many as 16.
“Lead times are just longer than they’ve ever been, and that’s just when the product is done,” he said. “And, in our industry, a manufacturer might usually come out with a price increase once a year. Now, they’re coming out with increases maybe once a month.”
Marsh Electronics distributes electromechanical supplies for more than 300 manufacturers; its regional distribution connects Minnesota, Illinois, Ohio, North Carolina and parts of Florida.
Lamping said a delay in just one component can shut down a production line, and the effects can be long-lasting.
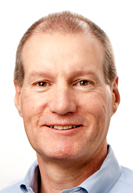
Westfield-based Altex, a custom manufacturer of wire harnesses and cable assemblies, is also feeling the impacts of the global s`hortage. President Rick Bromm said, if the circuit board with that silicon semiconductor chip is a brain, Altex’s wire and cable fixtures are the neurosystem that deliver the signal to its destination.
If Altex’s customers can’t get their hands on a circuit board, they don’t need Altex’s products. Without a confirmed order, manufacturing becomes less efficient. Deliveries of wires, cables, connectors and terminals that normally take around six weeks are now 18 to 20 weeks out. When they do show up, it’s a mad scramble to catch up.
Even when Altex finds the supplies it needs, Bromm said, he’s seen confirmed delivery dates pushed back as much as four weeks at the last minute.
“That makes it hard to do your forward planning,” he said.
Finding a way out
TMC is being forced onto the open market to find some parts, Mattice said, piecing orders together in small batches instead of buying in bulk. That forces its manufacturing customers to pay higher prices on top of TMC’s brokerage fees.
“It’s a lot of time and energy spent trying to solve those problems on our end,” Mattice said. “Now, it’s a regular way of life in satisfying production.”
But he predicted that the waning pandemic and vaccine penetration will eventually restore the supply chain.
Lamping is taking a personal approach to meeting the shortage head on, by meeting with Marsh Electronics’ top customers more frequently to get a better, more up-to-date sense of their needs. From there, he hopes to analyze trends and form a longer forecast.
“Before, it was, ‘Let us know what you’re going to do next quarter.’ Now, we need to look out six to eight months longer. It’s a matter of sitting down, looking at their requirements and demands, and making sure our supply chain matches demand for that,” he said.
Altex is taking a different approach. Bromm said his facilities have pivoted from long-range planning to a build-to-order environment.
“We work closely in weekly meetings with our customer base to pinpoint the real demand and what they really need to get their products out the door so we don’t use up any needed product in assemblies that are more urgent than others,” Bromm said. “As we focus on that, not everything is short. We continue to build other customer products that aren’t as in dire straits.”
Farrer said Allegion developed a system, after a lesser supply shortage roughly three years ago, that has helped it better deal with shortages this time around. Allegion now regularly updates its circuit-board design to weed out any components that might be obsolete and therefore harder to source.
The company also tracks which components of a circuit board are susceptible to shortages and compiles a list of potential qualified alternate vendors.
Still, Farrer said, Allegion can’t dual-source every part. That’s why the company has extended its forecasting from 12 months to 18.
“It’s just thinking farther down the road,” she said. “The demand cycle is different from what anybody has seen. The fact that we’ve already done that helps us; it has served us well as we sit here now.”
Though she couldn’t provide metrics to demonstrate it, Farrer said Allegion has also started increasing orders to create “safety stock” for lean times.
Cover your bases
Conexus Indiana’s Carpenter said extending forecasting alone won’t solve supply-chain problems on the scale the pandemic has brought. The lack of manufacturing diversity within the industry allowed this problem to snowball, he said, so advanced manufacturers need to broaden their supplier base, increase inventories and upgrade technology.
Many companies Conexus has heard from have “done six years of tech upgrades in six months because of what’s going on,” he said.
Increasing the number of U.S. semiconductor manufacturers could become an important factor in broadening the limited supply base. Carpenter said the Indiana Economic Development Corp. has even been in talks with Tower Semiconductors, an Israeli-based company with operations in Nevada, about bringing additional semiconductor manufacturing to Indiana.
Until then, silicon-semiconductor-related businesses in central Indiana are just looking to make enough changes to make it through to the other side.
“It’s full-court-press every single day by a talented group of people, quality managers managing to bring parts in,” Farrer said. “Hopefully, we can weather getting through this quarter and next quarter.”•
Please enable JavaScript to view this content.